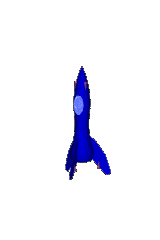
This thing doesn't work. Stay tuned for further development... Don't build it like below!
Though I have a large tow mixer I thought it would be nice to have a smaller mixer for smaller batches of papercrete. I had a lawn mower that was not being used, a plastic drum with a removable lid, and an old evaporative cooler with a 3/4" shaft and bushings. I started with a couple of sketches of possible designs.
I got some 1/8"x1" steel strap, some 1" square tubing, and some 1 1/2" angle iron to build the frame. First I made a ring from the 1/8"x1" strap to fit snugly into the top of the drum, cutting and welding the ends together. The mounting bolts on my lawn mower engine were in an irregular triangular layout, so I decided to use two parallel angle irons with two bolts through one of them and one bolt through the other. I mounted the engine (minus blade) on this framework and clamped the frame in the top of the drum.
I measured from the ring to the bottom of the drum. Since I wanted my blade to be about 10" above the bottom of the drum so I could bend it in a downward "V", I subtracted 10" and cut two 1" square tubes to fit. I welded these onto the angle iron holding the engine so that they were off center on the engine crankshaft to allow room for the lower bushing. Next two braces of 1/8"x1" strap were welded at a diagonal from the ring to the tubes.
I very carefully disassembled the evaporative cooler fan with a sledgehammer, salvaging the 3/4" shaft and saddle bushings. As luck would have it, the shaft was within an inch of the right length, so I elected to use it "as is" without cutting. I welded the blade mount bolt onto the end of the steel shaft so that it could be screwed into the engine crankshaft. On the other end of the shaft I welded a 3/8" stud and a large washer, to bolt on the blade. Alignment of these bolts with the shaft, and placement of the lower bushing are critical to prevent vibration later. I screwed the shafts together, slipped the bushing on the lower end, and bolted it to a piece of angle iron cut to fit between the square tubes. After adjusting the position of the bushing, I welded the angle iron to the tubes.
Next I cut four 10" pieces of the 1" square tubing and welded them at the quadrants of the ring so that they rested on the top of the barrel. On the two opposing ones I welded a handle made by bending 1/8" strap into a short "u" shape. Next to one of these handles I welded a mount for the engine speed control.
The blade was bent by heating with a torch. Then I mounted it on the lower end of the drive shaft, completing the assembly.
The final product is light enough to be lifted out of the barrel, and balances by one handle so that it can be hung from a hook when not in use.
Here's a bottom detail of the engine mount.
Here's the beast clamped down and ready to use.
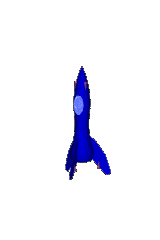